
Chain Drive Simulation
DIGITAL ENGINEERING AND EVALUATION
3D Virtual Validation Model
​For the development of a chain drive, it is essential to have not only knowledge of the physical properties of the chain but also precise understanding of the excitations of all components involved in the chain drive, such as camshafts, the crankshaft, and other drive elements like high-pressure pumps. To accurately and realistically consider these excitations in the early phases of development, the use of comprehensive engine simulation with a digital twin is necessary. This approach ensures that all interactions between the subsystems are fully considered.
This engineering approach
-
Ensures that the predictions of chain drive and overall system dynamics are as accurate as possible, even before physical prototypes and measurements are available
-
Offers analysis and evaluation of complete chain dynamics and powerloss within the powertrain context
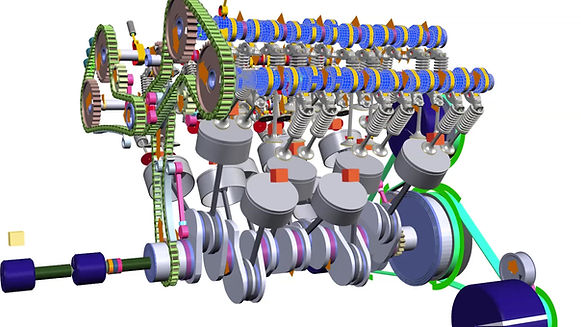
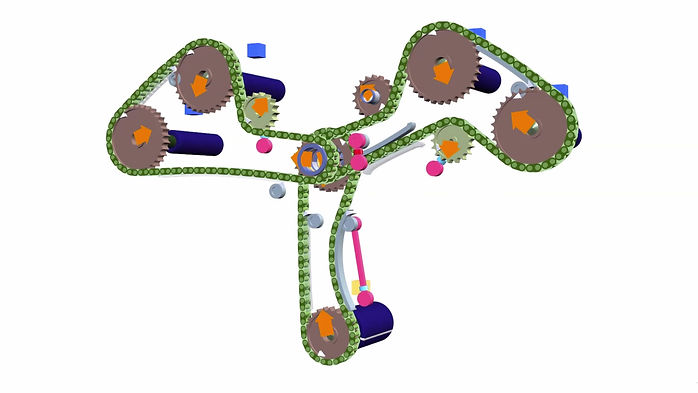
Parameter Study
1D Torsional MBS Model
The modular structure of the 3D Validaton
Model allows the chain drive submodel to be used directly for optimization on the basis of a fast torsional model with automatically generated excitation maps.
​
-
The physical and geometric parameterization of the chain drive is completely adopted, thus avoiding input errors
-
The parameters identified during the optimization process for the chain drive are tested and validated in the 3D Validaton Model, taking into account all degrees of freedom.
Oval pulley - Chain drive dynamics
Comparative analysis of chain forces when using circular and oval crankshaft sprocket, taking into account different camshaft phasing for intake and exhaust
-
4 cylinder chain layout - 350N pretension
-
Nominal position (0° displacement) for both cam phaser
-
Comparison between circular and oval pulley at crankshaft shows shifting of critical system behavior


Chain drive transversal deflection
Analysis of dynamics and acoustics of a stopper element using circular and oval sprockets on the crankshaft ​
-
Flexible guide rail modeled as a stopper element for high transversal deflections
-
No continuous contact between chain and upper guide rail
-
Contact force and speed range between upper guide and chain is increased with oval crankshaft sprocket
Advanced Chain Simulation
System analysis using flexible guides.
Optimizing chain guide design.
​
-
Flexible guide rail comparison for tensioner side
-
Variation in number of partitions
-
Stress analysis and deflection comparison during resonance passing
-
Additional fin leads to a reinforcement of the rail for analyzed speed step
